エラストマー・高機能材料両輪に
グローバルで事業を拡大 20年に売上高5000億円へ
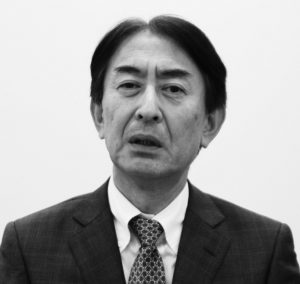
田中公章社長
日本ゼオンは2020年のありたい姿を「化学の力で未来を今日にするZEON」とし、具体的な数値目標として連結売上高5000億円を掲げている。その目標達成に向け、現在は14~16年度を対象期間とする中期経営計画「SZ―20フェーズⅡ」により、エラストマー素材事業(合成ゴム・合成ラテックス・化成品事業)と、高機能材料事業(化学品・情報材料・エナジー材料・医療器材事業)のそれぞれの強みを磨き上げ、両輪でグローバルに事業を拡大させることを基本戦略として、取り組みを推進しているところだ。
■エラストマー事業
SZ―20フェーズⅡでは、エラストマーの事業戦略として「成長市場へのグローバルな対応による強い事業のさらなる強化」を設定。具体的には「S―SBRの2拠点体制の確立」「ゼットポールの高耐熱性新製品の採用拡大」「バイオ合成ヒドリンゴムの上市」「手袋用NBRラテックス」「C5ケミカル事業の拡大戦略」を進めている。
S―SBRについては、徳山工場に続きシンガポール工場を建設し、4月から第2系列を稼働させたことで、2拠点体制を確立することができた。シンガポール工場は14年4月に年産3万5000tの第1系列が竣工。これに第2系列の同3万5000tが加わったことで、同工場の生産能力は同7万tとなった。
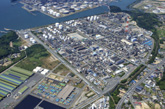
水島工場
さらに、徳山工場の同5万5000tを加えると、同社のS―SBRは同12万5000tにまで拡大している。
この2工場について、同社では徳山工場を新製品の開発拠点として位置付け、差別化製品を生産、シンガポール工場に関しては需要増に対応し、量産品を中心に生産を行う拠点とするとの方向性を打ち出した。
一方、製品に関しては、非油展品は同社の従来品に対し、省燃費性の大幅改善が期待できる製品を主力化、油展品については他社に対して性能優位性がある既存品の拡販と、新製品を継続して投入していく戦略を示している。
ゼットポールの高耐熱性新製品は、これまで130℃前後だった耐熱性を150℃程度まで向上させたものだ。この結果、ガスケットやシールなどの寿命を2~3倍延ばすことが可能となり、成長が期待できる製品として採用の拡大を図っている。
バイオ合成ヒドリンゴムは、トヨタ自動車のバキュームセンシングホースに4月から採用された。ゴム全体の植物由来原料が4割弱になることと、一部品当たりのCO2を3tほど削減できる、環境負荷の低いゴムである。トヨタは、このゴムを高い耐油性と耐熱性が必要な特殊ゴム製部品であるエンジン・駆動系ホースに世界で初めて採用した。
トヨタでは、さらにブレーキ系ホースや燃料系ホースなどにも採用を拡大していく方針を示している。
手袋用NBRラテックスについては、市場が年率7%で成長しており、今後も同じような成長が続くと見られている。その中で、同社では医療用薄膜として欧州規格値を満たす製品を開発した。すでに最大手手袋メーカーで採用が決定するとともに、現在、複数社で評価実施中である。
同製品は、さらに架橋剤である酸化亜鉛の添加量を減らしても、同社従来品と同等の破断強度が得られることから、食品加工用にも展開しているところだ。
C5ケミカル事業については、世界の粘着テープ市場は年率5~6%の成長、世界の紙おむつ市場も年率6%の成長を続ける中で、同社のSISが使われ、拡大してきている。
これに対応するため能力増強を実施し、5月には水島工場の生産能力を年産4万2000tから同6万tに拡大した。
そのうち、独自製品である非対称SISは、エラスティックフィルムと粘着ラベルで採用され、使用量が拡大。フレキソについても予定通り、年明けから実機のテストが始まり、販売が可能になった。
それ以外にも保護フィルム、粘着テープ、ホットメルト粘接着でも使用が見込まれており、今後幅広い用途で採用が進んで行くことが期待されている。
■高機能材料事業
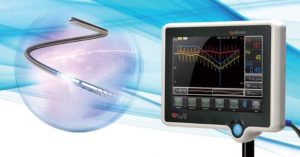
FFRデバイス
高機能材料事業については「重点3事業分野での研究加速による事業拡大」を事業セグメント別戦略として設定した。3事業分野とは、情報用部材